OSHA Updates: crystalline silica safety on the job
In 1970, the U.S. Congress created the Occupational Safety and Health Administration (OSHA) in an effort to ensure safe and healthy working conditions for working men and women. One of OSHA’s most important responsibilities is to set and enforce workplace safety standards, which describe the methods that employees must use to protect their workers from hazards. These standards are established after many worksite inspections, and they therefore evolve and change. Supervisors and employees must constantly be made aware of new OSHA requirements to avoid any violations, and, more importantly, to avoid employee injuries, health problems, or fatalities.
While OSHA is committed to preventing injuries and fatalities that occur in the workplace, the agency also works to reduce hazards that pose long-term, rather than immediate, threats to employees’ wellbeing. This is especially true when it comes to OSHA’s efforts to reduce the harmful effects of exposure to crystalline silica dust. Silica is a natural component of quartz, sand, and other minerals, and it becomes harmful to humans when workers chip, cut, drill, or grind objects that contain it, thereby creating small enough particles that can be inhaled.
According to OSHA, silica dust has been classified as a lung carcinogen, and it can cause silicosis, a dangerous lung disease that can appear years after exposure. It is estimated that more than 2.3 million workers in the United States are potentially exposed to dust containing crystalline silica, with nearly 90% of those workers employed in the construction industry. In an effort to protect these employees, OSHA has established a new regulation, 29 CFR 1926.1153, which requires contractors to limit their employees’ exposure to respirable crystalline silica.
OSHA’s new rule on respirable crystalline silica mandates reducing exposures through engineering and work practice controls. Additionally, it gives contractors flexibility by providing three different compliance options. Employers who follow the requirements fully and completely will not have to do air monitoring and will be assumed to be below the permissible exposure limit.
The first step to being in compliance with the new regulation is to identify a “silica competent person,” and ensure they are trained appropriately. A silica competent person is an individual who is capable of identifying existing and foreseeable respirable crystalline silica hazards in the workplace and who has authorization to take prompt corrective measures to eliminate or minimize risks. Secondly, employers may need to undergo an exposure assessment, followed by the full and proper implementation of all required safety controls.
The new regulation contains an extensive and detailed table which outlines the exposure control methods employers must use when their employees are working with materials that contain crystalline silica. Some of the highlights of the new regulation include:
- Identifying common construction tasks that might expose workers to silica dust and specify appropriate and effective engineering controls, work practices, and respiratory protection for each task performed.
- Performance Monitoring: assess the 8-hour Time Weighted Average (TWA) exposure based on air monitoring data and other objective data.
- Scheduled Monitoring: initial monitoring is used to assess the 8-hour TWA exposure based on personal breathing zone (PBZ) air samples.
Other steps to help keep one in compliance may include:
- Conducting exposure assessment of workers
- Develop the written exposure control plan
- Implement the exposure control plan
- Conduct frequent and regular inspections of the jobsite and modify the plan as conditions change
- Call in qualified persons to support the silica competent person with complex or unique situations
- Review the plan at the end of the project for lessons learned and incorporate them into future plans
It is important that all business owners who have employees who work with materials that contain silica be aware of OSHA’s new regulation, fully understand its requirements, and implement its compliance directives. This brief overview of 29 CFR 1926.1153 is only meant as a first step in this process. Below are links to important OSHA resources which will give employers a more complete understanding of the new regulation.
Resources:
OSHA Data & Statistics: https://www.osha.gov/oshstats/commonstats.html
OSHA Health Hazard Information on Crystalline Silica Exposure:https://www.osha.gov/Publications/osha3176.html
OSHA 29 CFR 1926.1153: https://www.osha.gov/laws-regs/regulations/standardnumber/1926/1926.1153
This Post Sponsored By
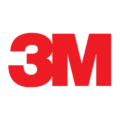
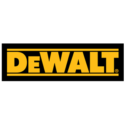
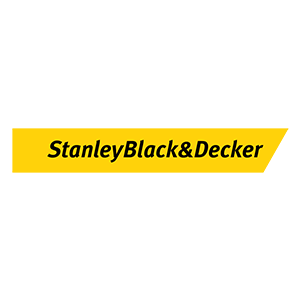
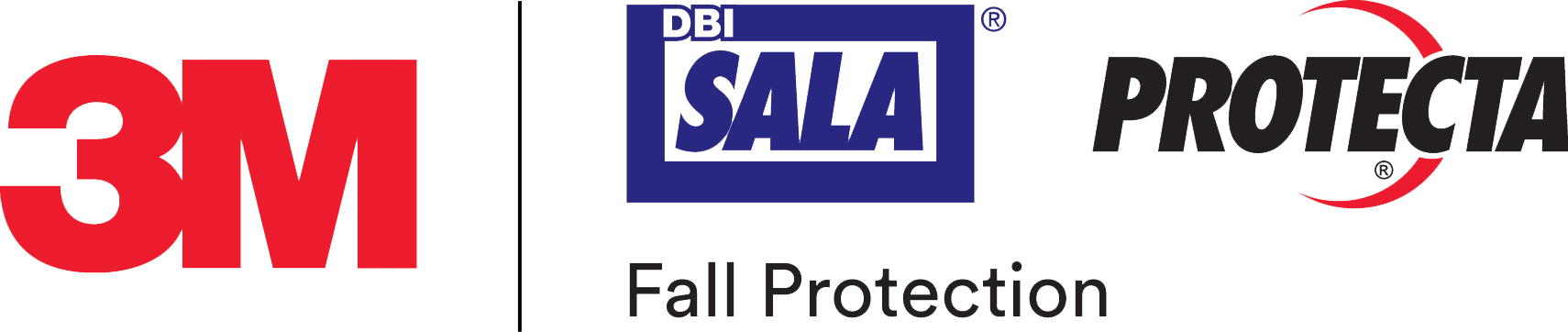