How to Meet OSHA Workplace Safety Requirement During COVID-19
This year, workplace safety has become a top priority for all U.S. employers. Covid-19 has provided new challenges for businesses, as they seek to operate in accordance with OSHA’s requirement (https://www.osha.gov/laws-regs/oshact/section5-duties) that their workplaces be “free from recognized hazards that are causing or are likely to cause death or serious physical harm” to their employees.
The large majority of workers Industrial Supply serves are in fields in which they do not have the option to do their jobs from home. Those who are employed in industries like manufacturing, construction, mining, building maintenance, and utilities all provide critical services and products that keep our economy going and help our entire community. It is necessary that these employees feel safe while doing so.
Since February, state and federal OSHA departments have received more than 32,000 coronavirus-related complaints (https://www.osha.gov/enforcement/covid-19-data#summary_data), demonstrating the challenges that Covid-19 poses to workplace safety. OSHA has created new resources (https://www.osha.gov/SLTC/covid-19/) and standards (https://www.osha.gov/SLTC/covid-19/standards.html), and employers must conduct regular compliance trainings to meet those regulations and maximize workplace safety in a changing environment.
In the past 6 months, businesses have had to take a number of measures to ensure the safety of their employees, such as:
Purchasing new types of safety products
While employers should be well aware of the safety equipment their employees need to reduce fall, chemical, heat and other hazards specific to their jobs, Covid-19 introduced workplace risks never before considered. Businesses have therefore had to incorporate new Personal Protective Equipment and other safety products, such as health screening tools, hand washing stations, touchless faucets, and specific janitorial supplies, into their procurement plans.
Decreasing the use of shared tools and equipment
The Center for Disease Control recommends (https://www.cdc.gov/coronavirus/2019-ncov/community/organizations/construction-workers.html) limiting tool sharing for workers in the construction industry as a way to minimize the risk of spreading Covid-19 on the job site. Creating individual tool boxes and consistently sanitizing shared equipment between users have become the new normal in many business routines.
Considering new ways to distribute safety products
It is critical that businesses do not run out of PPE, such as masks, eye protection, and hand sanitizer, and that these items are readily available to all employees. Businesses must consider all ways to accomplish this, such as providing industrial vending machines, which provide point-of-use inventory management for the industrial and safety supplies that employees depend on.
Adding safety evaluations and employee trainings
The risks that coronavirus pose to workers’ health and well-being has required employees to take on new roles, practice new routines, and use new technical skills. At the same time, employers must comply with new safety standards that have been developed to minimize those risks. Businesses have therefore had to continuously evaluate their safety plans and retrain their workers.
The unprecedented nature of this pandemic has forced businesses to consider these safety measures with little notice, and to do so at a time when their own financial futures may be uncertain. At Industrial Supply, comprehensive safety services have always been a significant component of our work, and we are committed to helping our clients navigate and respond to the shifting risks and requirements their industries are currently facing.
This Post Sponsored By
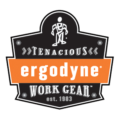
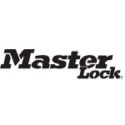
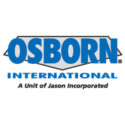
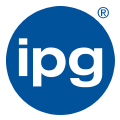