Metalwork 101: A Brief Survey from Industrial Supply Company’s Metalworking Services
Broadly defined as the forming and shaping of metal, humans have engaged in metalworking for thousands of years, both for ornamental and utilitarian purposes. Today, it’s pretty much impossible to find a field that is not reliant on metalwork. Industries as diverse as construction, mining, aerospace, and farming are all dependent on a diverse range of precisely shaped products that allow buildings to stand, coal to be extracted, airplanes to fly, and crops to be efficiently harvested.
The term metalwork refers to several different processes, including forming, in which a metal’s shape is changed without removing any material; joining, in which two separate pieces of metal are combined through welding, riveting, or other methods; and casting, in which molten metal is poured into a form. It is the fourth metalworking process, cutting, that we’re most interested in.
Just as it sounds, metal cutting is the process of using various tools to remove material in order to create a particular product. Over the years, people have developed different methods that are required for specific applications, such as:
- Turning: Using a lathe to turn a piece of metal, various tools are applied to the rotating piece to make grooves, cuts, and other marks with rotational symmetry.
- Milling: A milling machine holds a rotating cutting tool, such as a drill, borer, or threader, that is used on a metal piece set on a worktable that can move in multiple directions.
- Holemaking: Drills, punchers, or borers that are used by hand, on a lathe, or in a mill.
- Grinding: Also known as “abrasive cutting,” a grinding tool has a spinning wheel that uses abrasion to cut or polish.
Today’s machine shops take these old-school metalworking techniques to new levels. Multi-task machines can perform several different cutting processes, and they can run on pre-programmed software that directs their actions. The efficiency and accuracy of this type of production greatly exceeds what used to be accomplished manually.
The cutting element of the tools have also changed. Now, the majority of cutting tools are made with cemented carbide, a compound of carbon and a metallic element, like titanium or tungsten. This material works at higher temperatures, creates cleaner surfaces, and allows for faster machining than other materials, like steel. The drawback is that, while more effective, tools made with carbide are also more expensive. Thankfully, tool reconditioning services, like those we offer at Industrial Supply, can re-grind dull tools and get them back to their original condition for a fraction of the cost of a new tool.
Metalworking tools have changed since we first opened in 1916, and they continue to evolve to meet the needs of today’s businesses. Our customers can count on Industrial Supply to have a thorough knowledge of the industry, a vast network of trusted metalwork vendors, and the ability to create a metalwork plan that is customized to their particular operations.
Industrial Supply Center’s Salt Lake City headquarters is an Authorized Weld Center, offering custom weld-to-length bandsaw blades from Lenox. For complete information about our Metalworking Services, contact Kerry Deppe kdeppe@indsupply.com or Nate Heap nheap@indsupply.com.
This Post Sponsored By
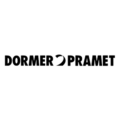
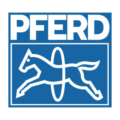
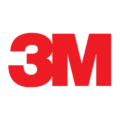
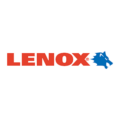