The Best Approach to Mitigating Workplace Hazards? “Find It and Fix It”
No matter the size of a business or the type of work involved, hazards to employees’ health and well-being exist in all workplaces. The challenge for every company is to identify potential and existing risks, and address them before their workers are negatively impacted.
Any good business owner understands they have a vested interest in protecting their employees. As the Occupational Safety and Health Administration (OSHA) states in Recommended Practices for Safety and Health Programs, workers are a business’s “most valuable asset.” Employee injuries or illnesses can disrupt productivity, harm workplace morale, increase employee turnover, and damage an employer’s reputation.
Unfortunately, it’s not always obvious what hazards exist in a particular workplace, which is why it’s important for business owners to set up a process to recognize and anticipate anything that could cause injury or illness. Who should be involved in this process? Leadership is very important in setting workplace safety as a fundamental company value and an integral part of how it does business. By modeling safe practices and actively seeking input about potential or existing hazards, management demonstrates its commitment to safe workplace practices.
But no safety program will ever be effective unless employees are part of finding potential problems and coming up with their solutions. The workers’ daily, hands-on experiences provide them with a strong awareness of any safety or health concerns. And, as OSHA notes, they also have the most to gain from hazard mitigation and the most to lose if any risks are not properly addressed.
OSHA has some ideas about how a business can include its employees as it works to find and fix workplace hazards. These include:
- Creating a clear process for employees to report any existing or potential hazards, injuries, illnesses, close calls, or safety and health concerns, and making sure employees know they can make these reports without fear of retaliation.
- Soliciting employee input on potential safety and health consequences before making significant changes in the workplace, such as adding new equipment or materials, or implementing major changes in staff organization.
- Training workers on how to identify and respond to hazards, and asking for and responding to their solutions for mitigating any risks.
It also can be very helpful for businesses to bring in an outside safety professional, who may be able to identify potential hazards that those within the company are unable to see. That person can make a complete hazard assessment and conduct employee safety trainings that are tailored to a business’s particular needs. Industrial Supply Company does this regularly for its customers on a variety of safety issues, including fall protection awareness, eye and hand protection, gas detection, hearing protection, and respiratory protection.
June is officially National Safety Month, but workplace safety is an issue that must be a priority all year long. For over 100 years, Industrial Supply has helped its customers identify and assess workplace hazards, and has provided them with the products and expertise they need to fix them. We’re ready to be your Safety Partner.
This Post Sponsored By
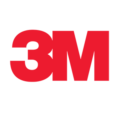
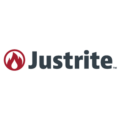
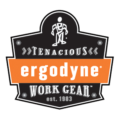
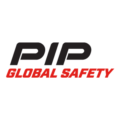